Decoding Your Whirlpool Washer: Understanding FxEx Error Codes
Seeing an error code flashing on your Whirlpool washing machine can be confusing. Codes starting with “F” followed by a number and “E” (like F1E1, F5E2, etc.) indicate specific faults detected by the machine’s control system. This guide will help you understand what these Whirlpool washer FxEx error codes mean and provide troubleshooting steps you can try.
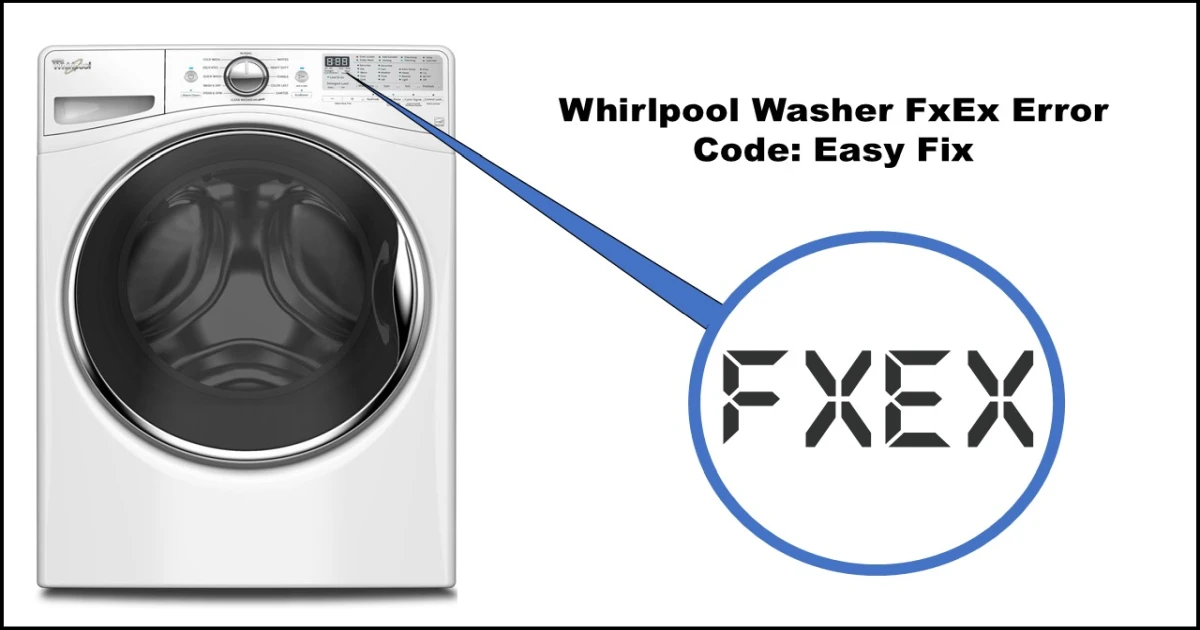
❗ IMPORTANT SAFETY FIRST ❗ Before attempting any inspection, cleaning, or repair that involves opening the machine’s panels or handling electrical components:
- Disconnect the washer from the power outlet.
- Turn off the water supply at both the hot and cold taps connected to the washer. Failure to do so can result in electric shock or water damage. If you are uncomfortable performing any of these checks, please contact a qualified appliance repair technician.
Understanding Your Whirlpool Washer FxEx Error Codes
Error Code F0E1: Load Detected During Clean Cycle
- Meaning: The washer senses laundry in the drum during the “Clean Washer” cycle, which should be run empty.
- Solution:
- Ensure the washer is unplugged.
- Open the door and remove any items from the drum.
- Close the door, plug the washer back in, and clear the error code (usually by pressing Cancel or Power).
- Restart the “Clean Washer” cycle with an empty drum.
Error Code F0E2: Excessive Suds Detected
- Meaning: The washer has detected too much foam (suds) during the cycle, which can prevent proper draining and spinning.
- Potential Causes:
- Using too much detergent.
- Using non-HE (High Efficiency) detergent in an HE machine.
- A blockage or restriction in the drain pump or hose.
- A blocked air chamber or pressure sensor hose, preventing accurate water level detection.
- Troubleshooting Steps:
- Use the Right Detergent: Always use HE detergent in HE washers. Check your detergent packaging for the correct dosage based on load size and water hardness.
- Run a Rinse/Spin Cycle: Try running a rinse and spin or drain and spin cycle to help clear out excess suds and water.
- Check Drainage: (Unplug washer first) Inspect the drain hose for kinks or blockages. Check the drain pump filter (usually accessible via a small panel at the bottom front) for debris and clean if necessary.
- Check Pressure System: (Unplug washer first) Inspect the pressure sensor hose (a thin tube usually running from the tub to the control board area) for kinks, leaks, or blockages. Check the air chamber (where the hose connects to the tub) for buildup.
Error Code F0E4: Water Temperature Error (Too Hot)
- Meaning: The incoming water temperature is incorrect, often too hot when cold is expected.
- Potential Causes:
- The cold water inlet hose is mistakenly connected to the hot water faucet.
- The water temperature sensor (NTC) is faulty.
- The main control board has a stuck heater relay (less common).
- Troubleshooting Steps:
- Check Hose Connections: (Turn off water supply first) Verify that the inlet hose marked “Cold” is connected to the cold water tap and “Hot” to the hot tap.
- Test NTC Sensor: (Unplug washer first) Using a multimeter, check the resistance of the NTC sensor. It should read approximately 9.8kΩ at 86∘F (30∘C). If the reading is drastically different, the sensor may need replacement.
- Inspect Main Board: (Requires technical skill) If the sensor is okay, the issue might be a stuck heater relay on the main control board, requiring board replacement.
Error Code F0E5: Unbalanced Load Detected
- Meaning: The load inside the drum is unevenly distributed, preventing the washer from spinning safely at high speeds.
- Solution:
- Pause the cycle or wait for it to end.
- Open the door and redistribute the laundry more evenly around the drum. Avoid washing single, heavy items (like a bath mat) alone, as they are difficult to balance. Add a few towels to help balance such loads.
- Close the door and restart the spin cycle or the entire wash cycle.
- If the error persists frequently even with well-distributed loads, there might be an issue with the suspension system or, rarely, the control board.
Error Code F1E1: Main Control Board Memory Error (EEPROM)
- Meaning: The main control board is having trouble reading its internal memory (EEPROM), which stores cycle information and settings.
- Troubleshooting Steps:
- Power Cycle: Unplug the washer, wait 2-3 minutes for the internal capacitors to discharge, then plug it back in. Check the outlet voltage if possible. Try restarting the cycle.
- Replace Main Board: If the error reappears consistently, the main control board likely needs to be replaced.
Error Code F1E2: Motor Control Unit Voltage Error
- Meaning: The separate Motor Control Unit (MCU, if equipped) has detected incoming power voltage that is too low.
- Troubleshooting Steps:
- Check Power Supply: Verify your home’s electrical outlet is providing the correct voltage. Try plugging the washer into a different outlet if possible (ensure it’s properly rated). Avoid using extension cords.
- Replace MCU/Main Board: (Requires technical skill) If the voltage supply is normal, the fault lies within the Motor Control Unit or potentially the main board. Replacement may be needed.
Error Code F1E4: Main Board Relay Error
- Meaning: A relay on the main control board is detected as stuck open or closed.
- Solution:
- Replace Main Board: This error typically indicates a failure on the main control board itself, requiring replacement.
Error Code F2E3: Control Board / User Interface Mismatch
- Meaning: The main control board and the user interface (the panel with buttons/display) are not communicating correctly or have incompatible software/firmware.
- Potential Causes:
- Loose or damaged wiring harness between the two boards.
- Corrupted firmware on one or both boards.
- Faulty main board or user interface board.
- Troubleshooting Steps:
- Check Connections: (Unplug washer first) Inspect the wiring harness connecting the main control board to the user interface board. Ensure connectors are secure and wires aren’t damaged.
- Replace Main Board: If connections are good, the main board is often the primary suspect.
- Replace User Interface: If replacing the main board doesn’t fix it, the user interface board may be the cause.
Error Code F3E1: Water Level System Error
- Meaning: The washer is having trouble detecting the correct water level. This can be caused by issues with the pressure sensor, drain pump, heater, or related wiring.
- Troubleshooting Steps:
- Check Drain Pump & Filter: (Unplug washer first) Ensure the drain pump isn’t running continuously when it shouldn’t be. Check the pump filter for obstructions. Clean the filter and ensure the drain hose is clear.
- Inspect Pressure System: Check the thin pressure switch hose for kinks, blockages, or damage. Ensure it’s securely connected at both the tub (air chamber) and the pressure switch/sensor. Clean the air chamber if accessible and potentially blocked.
- Check Wiring: Inspect connections between the pressure switch, main board, drain pump, and heating element (if related symptoms occur).
- Test Pressure Switch: (Requires technical skill) Check the pressure switch for proper operation.
- Replace Main Board: If all other components check out, the main board may be faulty.
Error Code F3E2: Wash Temperature Sensor (NTC) Error
- Meaning: The main control board detects that the wash water temperature sensor (NTC) reading is shorted or open (out of the expected range).
- Troubleshooting Steps:
- Check Wiring: (Unplug washer first) Inspect the wiring and connector between the wash NTC sensor and the main control board.
- Test NTC Sensor: Using a multimeter, check the resistance of the wash NTC sensor. It should be approximately 9.8kΩ at 86∘F (30∘C). Replace the sensor if the reading is incorrect.
- Replace Main Board: If wiring and the sensor are okay, the issue may be on the main board.
Error Code F3E5: Dry Temperature Sensor (NTC) Error (Washer-Dryer Models)
- Meaning: On models with a drying function, the main control board detects that the drying temperature sensor (NTC) reading is shorted or open.
- Troubleshooting Steps:
- Check Wiring: (Unplug washer first) Inspect the wiring and connector between the dry NTC sensor and the main control board.
- Test Dry NTC Sensor: Using a multimeter, check the resistance of the dry NTC sensor. It should be approximately 1.48kΩ at 68∘F (20∘C). Replace the sensor if the reading is incorrect.
- Replace Main Board: If wiring and the sensor are okay, the main board may be faulty.
Error Code F3E6: Accelerometer Error
- Meaning: The accelerometer, which helps detect drum movement and balance, is malfunctioning.
- Solution:
- Replace Main Board: This sensor is often integrated into the main control board. The typical solution is to replace the main board.
Error Code F4E1: Wash Heater Relay Error
- Meaning: The main control board is commanding the wash heater to turn on, but it’s not detecting the expected temperature increase (possibly due to a faulty relay not closing).
- Troubleshooting Steps:
- Check Heater Relay: (Requires technical skill) Test the heater relay function on the main board.
- Check Wiring/Connectors: (Unplug washer first) Ensure connectors to the heater and main board are secure and undamaged. Replace the harness if defective.
- Replace Relay/Main Board: If the relay itself is faulty, it usually requires replacing the entire main board.
Error Code F4E2: Heater Circuit Failure
- Meaning: The control board has detected a problem with the heating element circuit (e.g., open circuit, short circuit, or ground fault).
- Troubleshooting Steps:
- Check Wiring: (Unplug washer first) Inspect wiring and connectors to the heater, main board, and pressure switch (as water level detection is linked to heating). Reseat connectors, repair/replace damaged wires.
- Check Heater Resistance: Using a multimeter, check the resistance across the heater terminals. It should typically be between 18Ω and 28Ω. An “OL” or infinite reading means it’s open; 0Ω means it’s shorted.
- Check Heater Grounding: Check for continuity between each heater terminal and the machine chassis (ground). There should be no continuity (infinite resistance). If grounded, replace the heater.
- Inspect Heater: Visually inspect the heater for damage or signs of contact with the drum. Address any cause of contact (e.g., worn bearings). Check for water leaks around the heater mounting area.
- Check Pressure Switch: Verify the pressure switch is working correctly.
- Check Main Board: If the heater and wiring are okay, the control board might be faulty.
Error Code F4E4: Dry Fan Motor Error (Washer-Dryer Models)
- Meaning: On models with a drying function, an open or short circuit is detected in the drying fan motor.
- Troubleshooting Steps:
- Check for Blockage: (Unplug washer first) Ensure the fan motor and blade can rotate freely and are not blocked by lint or debris.
- Check Wiring: Inspect the wiring harness connection between the fan motor and the control board.
- Check Motor Resistance: Using a multimeter, check the resistance of the fan motor windings. It should be approximately 1800Ω.
- Check Fan Blade: Ensure the fan blade is intact and secure on the motor shaft.
- Replace Control Board: If the motor and wiring seem okay, the control board might be the issue.
Error Code F5E1: Door Switch Error
- Meaning: The control board cannot correctly detect whether the door switch is open or closed.
- Troubleshooting Steps:
- Check Door Closure: Ensure the door is firmly closed and latched. Listen for the click.
- Check Wiring: (Unplug washer first) Inspect the wiring harness connecting the door lock/switch assembly to the main board.
- Test Door Switch: Using a multimeter set to continuity or resistance, check the door switch contacts. It should show open circuit (OL / infinite Ω) when the door is open and closed circuit (near 0Ω, typically 0.1−1.0Ω) when the door is closed and latched.
- Replace Main Board: If the switch and wiring are okay, the fault may be on the main board.
Error Code F5E2: Door Lock Error
- Meaning: The control board attempted to lock the door at the start of a cycle but failed to confirm the lock engaged within the expected time (e.g., 20 seconds).
- Troubleshooting Steps:
- Check Door Closure: Ensure the door is fully closed without obstructions. Check the door hook and the lock mechanism alignment. Repair or replace bent/damaged mechanical parts.
- Check Wiring: (Unplug washer first) Inspect the wiring harness between the main board and the door lock assembly for damage, loose connections, or signs of overheating/corrosion (especially if leaks occurred).
- Check Lock Resistance: Using a multimeter, check the resistance of the door lock solenoid/actuator. It should typically be around 80Ω.
- Check Lock Voltage (Advanced): If comfortable and safe, check if the control board is sending voltage (e.g., 120V AC) to the lock solenoid when it tries to lock. If voltage is present but it doesn’t lock, replace the door lock assembly. If no voltage is sent, the main board might be faulty.
- Replace Lock/Board: Often requires replacing the door lock assembly. If the issue persists, the main board could be the cause.
Error Code F5E3: Door Unlock Error
- Meaning: The control board attempted to unlock the door at the end of the cycle but failed to confirm it unlocked within the expected time (e.g., 4 minutes). The door remains locked.
- Troubleshooting Steps:
- Wait and Retry: Sometimes residual water pressure or slight misalignment can prevent unlocking. Wait 5-10 minutes after the cycle should have ended, then try gently pushing on the door near the lock mechanism while the machine attempts to unlock (or after pressing Cancel).
- Check for Board Issue: (Unplug, wait, replug) Close the door, turn the washer ON, press and hold Cancel/Reset for >3 seconds, then turn OFF without starting a cycle. Does the door lock engage? If yes, the main board might be incorrectly keeping the lock energized and needs replacement.
- Replace Lock Assembly: If the board seems okay, the door lock mechanism itself is likely jammed or faulty and needs replacement. Also, re-check door alignment (hinges, hook).
Error Code F5E4 (“dr”): Door Not Opened Error
- Meaning: This code often appears if:
- The Start button is pressed while the door is detected as open.
- The door hasn’t been opened between several consecutive cycles.
- The control board has issues detecting the door switch status (related to F5E1).
- Solution:
- Ensure the door is properly closed.
- Open and close the door firmly to reset the switch detection.
- If the error persists, troubleshoot as per F5E1 (Door Switch Error), F5E2 (Door Lock Error), and F5E3 (Door Unlock Error) as the underlying cause is likely related to the door lock/switch system.
Error Code F6E1: Main Board / Motor Control Communication Error
- Meaning: (Applies to models with a separate Motor Control Unit – MCU) The main control board (ACU/CCU) and the MCU are not communicating correctly.
- Troubleshooting Steps:
- Check Wiring: (Unplug washer first) Inspect the wiring harness and connectors between the main board and the motor control unit. Ensure they are secure and undamaged.
- Check Door Switch: A faulty door switch can sometimes interrupt communication pathways. Test as per F5E1.
- Check Motor: Test motor windings resistance (typically 8−22Ω) and check for blockages.
- Replace MCU/Main Board: If wiring and motor are okay, either the MCU or the main board is likely faulty and needs replacement.
Error Code F6E2 / F6E3: Main Board / User Interface Communication Error
- Meaning: Communication between the main control board (CCU) and the user interface (UI) board has failed (F6E2: CCU to UI, F6E3: UI to CCU).
- Troubleshooting Steps:
- Power Cycle / Clear Code: Try unplugging the machine for a few minutes, then plug back in and attempt to clear the code via the control panel.
- Check Wiring: (Unplug washer first) Inspect the wiring harness and connectors between the main board and the user interface board. Reseat connectors and check for damage.
- Replace User Interface: If wiring is okay, the user interface board might be faulty.
- Replace Main Board: If replacing the UI doesn’t help, the main control board is the likely cause.
Error Codes F7E1 – F7EC: Motor / Speed Sensing Errors
- Associated Codes: F7E1 (Tachometer Signal), F7E2 (MCU Over Temp), F7E3 (MCU Over Current), F7E4 (Motor Over Temp), F7E8 (Motor Disconnected), F7E9 (Motor Locked), F7EA (Motor Phase Missing), F7EC (Motor Overloaded).
- Meaning: These codes relate to problems with the drive motor, its speed sensing (tachometer), or the motor control unit detecting abnormal conditions like overheating or excessive current draw. F7E1 specifically means the control board isn’t getting a proper speed signal from the motor’s tachometer.
- Potential Causes:
- Drum is blocked (e.g., laundry caught between drum and tub).
- Severe overload or running multiple heavy cycles consecutively causing overheating.
- Loose or damaged wiring between the motor and the control board(s).
- Faulty motor (windings, bearings, thermal protector).
- Faulty tachometer on the motor.
- Faulty Motor Control Unit (MCU) or Main Control Board.
- Troubleshooting Steps:
- Check for Blockages: (Unplug washer first) Rotate the drum by hand. Does it turn freely? Check for obstructions or binding. Listen for grinding noises (bad bearings).
- Check Load: Ensure the machine isn’t severely overloaded. Allow cooldown time between heavy cycles, especially in high ambient temperatures.
- Check Wiring: Inspect the wiring harness and connectors between the motor and the main board/MCU. Look for loose pins, chafed wires, or burn marks.
- Test Motor: Using a multimeter, check the resistance of the motor windings (typically 8−22Ω). Check the tachometer resistance separately (value varies by model, look for consistency or consult service manual).
- Replace Motor/Control Board: If wiring is good and the motor tests faulty or symptoms point strongly to it, replace the motor. If the motor seems okay, the issue might be the MCU (if separate) or the main control board.
Error Code F8E0: Steam Valve Error (Steam Models)
- Meaning: On models with a steam feature, there’s an issue with the steam inlet valve or water supply to it.
- Troubleshooting Steps:
- Check Water Supply: Ensure the water tap supplying the steam valve is fully open and has adequate pressure. Check any inline filters for blockages.
- Check Wiring: (Unplug washer first) Inspect the harness connection between the steam control unit/main board and the steam valve.
- Check Hoses: Ensure hoses connected to the steam generator/valve are secure and not leaking.
- Test Steam Valve: Using a multimeter, check the resistance of the steam valve coil. It should be approximately 980Ω.
- Check Steam Control/Main Board: If the valve and wiring are good, the control unit might be faulty.
Error Code F8E1: Water Fill Timeout / Inlet Valve Error
- Meaning: The washer didn’t detect the water level reaching the required point within the allotted time (e.g., 6 minutes).
- Potential Causes:
- Water taps are closed or not fully open.
- Inlet hoses are kinked or blocked.
- Inlet valve screens (filters) are clogged.
- Drain hose siphoning water out as it fills.
- Pressure hose kinked/blocked, preventing level detection.
- Faulty water inlet valve(s).
- Faulty main control board.
- Troubleshooting Steps:
- Check Water Supply: Ensure both hot and cold taps are fully open. Check hoses for kinks.
- Clean Inlet Screens: (Turn off water supply first) Disconnect hoses from the back of the washer. Check the small filter screens inside the valve connections and clean any debris. Also check screens at the tap end of the hoses.
- Check Drain Hose Position: Ensure the drain hose has an air gap and is installed at the correct height (refer to manual) to prevent siphoning.
- Check Pressure System: Inspect the pressure hose and air chamber for blockages or kinks.
- Check Wiring: Inspect wiring to the water inlet valves.
- Test Inlet Valves: Using a multimeter, check the resistance of the water inlet valve coils. Each should be approximately 980Ω. Replace if faulty.
- Replace Main Board: If valves and pressure system are okay, the main board may be the cause.
Error Code F8E2: Dispenser Motor Error
- Meaning: The motor that positions the detergent dispenser drawer (for different compartments like pre-wash, main wash, softener) is unable to reach the correct position.
- Troubleshooting Steps:
- Check Wiring: (Unplug washer first) Inspect the wiring connection to the dispenser motor.
- Test Dispenser Motor: Using a multimeter, check the resistance of the dispenser motor (approx. 1580Ω).
- Check Switch/Voltage (Advanced): Check if the dispenser position switch is functioning and if the motor is receiving voltage from the main board when it should move. If voltage is present but no movement, replace the dispenser motor assembly. If no voltage, suspect the main board.
Error Code F8E3: Overflow Condition
- Meaning: The washer has detected a water level that is too high (overflow condition), likely due to the pressure switch’s overflow contact being closed repeatedly. The drain pump will usually run continuously or intermittently, and the door remains locked.
- Potential Causes:
- Water inlet valve stuck open, continuously letting water in.
- Excessive sudsing (too much detergent) tricking the pressure sensor.
- Drain pump or hose blocked, preventing water from leaving effectively.
- Faulty pressure switch (stuck overflow contact).
- Air leak in pressure switch hose or blocked air chamber.
- Main board fault (e.g., stuck drain pump relay/TRIAC).
- Internal leak filling the base/drip tray and activating a floater switch (if equipped).
- Troubleshooting Steps:
- Check Inlet Valve: (Turn off water supply after observing) Does water keep entering the drum even when the washer is paused or off? If so, the inlet valve is stuck and needs replacement.
- Check for Suds: Is there excessive foam? Address detergent usage (see F0E2).
- Check Drainage: Ensure the drain hose and pump filter are clear.
- Check Pressure System: Inspect the pressure switch, hose, and air chamber carefully for faults, blockages, or leaks.
- Check for Leaks: Look for signs of water leaks inside the machine, especially in the base if it has a flood protection switch.
- Check Main Board/Switch: If other checks pass, the pressure switch or the main board could be faulty.
Error Code F8E4: Flowmeter Error
- Meaning: (On models equipped with a flowmeter to measure incoming water) The control board isn’t receiving the expected signal from the flowmeter.
- Troubleshooting Steps:
- Check Inlet Valve: Ensure the water inlet valve is opening correctly.
- Check Wiring: (Unplug washer first) Inspect the wiring between the main board and the flowmeter.
- Check Flowmeter Voltage (Advanced): Verify the flowmeter is receiving the correct DC voltage (often +5Vdc) from the main board. If voltage is present but no signal, replace the flowmeter. If no voltage, suspect the main board.
Error Code F9E1: Drain System Error
- Meaning: The washer is having trouble draining the water, or it cannot confirm that the water has been drained within the expected time.
- Potential Causes:
- Drain pump filter clogged with debris.
- Drain hose kinked, blocked, or installed improperly (e.g., too high).
- Excessive suds slowing down draining.
- Object blocking the pump impeller.
- Faulty drain pump (not running or running weakly).
- Blocked air chamber or pressure hose preventing the system from sensing the water level has dropped.
- Faulty pressure switch.
- Faulty main control board or wiring issue to the pump.
- Troubleshooting Steps:
- Check Drain Filter & Hose: (Unplug washer first) This is the most common cause. Thoroughly clean the drain pump filter. Check the entire length of the drain hose (inside and outside the machine) for kinks or blockages.
- Check for Suds: Address detergent usage if over-sudsing is suspected.
- Check Pump Impeller: (Carefully, with filter removed) See if you can manually turn the small pump impeller. Check for obstructions like hairpins, strings, etc.
- Check Pressure System: Inspect the pressure hose and air chamber for blockages.
- Check Wiring: Inspect wiring connections between the drain pump and the main board.
- Test Drain Pump: Check the electrical resistance of the drain pump (approx. 18Ω). Listen if it hums or tries to run during the drain cycle. Replace if faulty.
- Test Pressure Switch: Verify the pressure switch correctly senses when the tub is empty.
- Replace Main Board: If all other components related to draining and water level sensing are okay, the main board might be faulty.
When to Call a Professional
While some FxEx errors can be resolved with simple steps like cleaning filters or adjusting loads, many involve testing components with a multimeter or replacing parts like control boards, motors, or sensors. If you’ve performed the basic checks and the error persists, or if you’re not comfortable working with electrical components and wiring, it’s best to contact a qualified Whirlpool appliance repair technician. They have the diagnostic tools and expertise to safely and accurately repair your washing machine.