Understanding Your Beko Washing Machine: Error Codes Explained
Beko washers are designed to communicate issues directly to you via error codes displayed on the control panel.
Understanding these codes is the first step to diagnosing and potentially fixing the problem, getting your laundry routine back on track. This guide will help you decipher common Beko washing machine error codes, suggest simple troubleshooting steps you can try, and indicate when it’s time to call a professional.
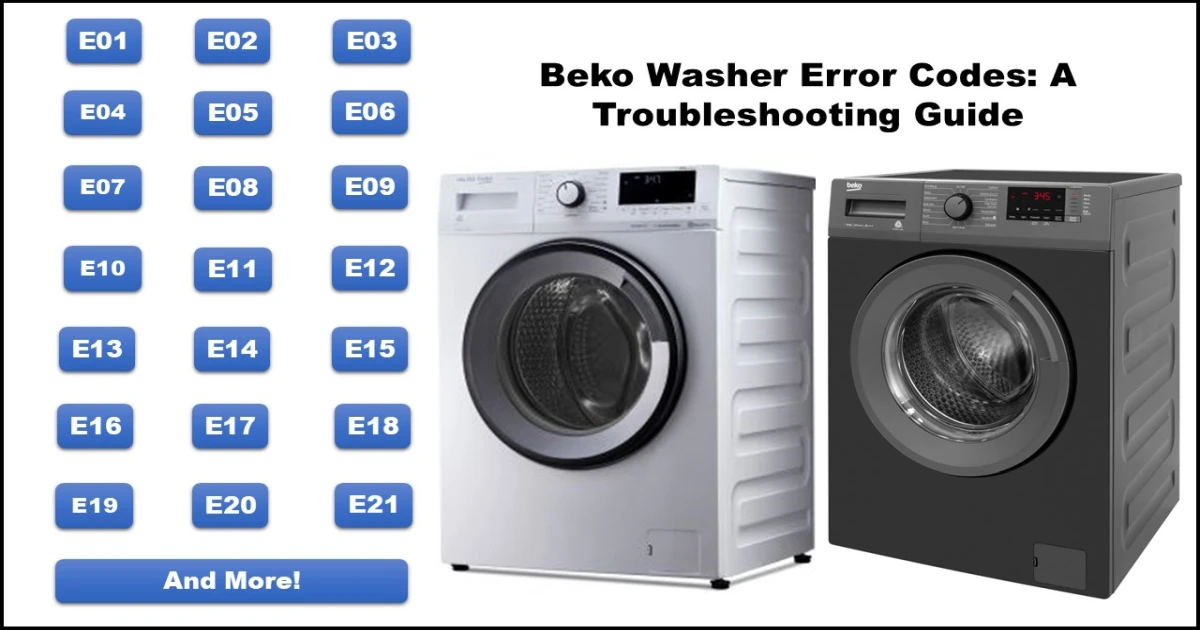
IMPORTANT SAFETY FIRST: Before attempting any checks or troubleshooting involving opening panels or inspecting components, always disconnect your washing machine from the power outlet to prevent electric shock. If you are ever unsure or uncomfortable performing a check, contact a qualified appliance repair technician.
Before Diving into Specific Beko Washing Machine Error Codes: Quick Checks
Sometimes, washing machine issues aren’t due to a major fault. Before assuming the worst based on an error code, try these simple steps:
- Power Cycle: Turn the machine off at the power button, wait a minute, then unplug it from the wall socket. Wait another 5-10 minutes, plug it back in, and turn it on. This can sometimes reset minor electronic glitches.
- Water Supply: Ensure the water taps connected to the machine are fully open and that the inlet hoses aren’t kinked or crushed.
- Drain Hose: Check that the drain hose isn’t blocked, kinked, or positioned too low or too high (refer to your Beko manual for correct height).
- Filter: Locate and clean the drain pump filter (usually behind a small flap at the bottom front of the machine). Obstructions here are a very common cause of draining issues (like E05).
- Load Balance: An unevenly distributed load (e.g., one heavy towel) can prevent the machine from spinning correctly (triggering E18). Try redistributing the clothes.
- Door: Make sure the door is firmly closed and latched. Check that no clothing is caught in the seal, preventing it from locking properly (related to E09/E10/E23/E28).
If these basic checks don’t resolve the issue or clear the error code, let’s look at what specific codes might mean.
Common Beko Washing Machine Error Codes
Here’s a breakdown of common error codes, their potential causes, and suggested actions:
E01: NTC Sensor Error
- Meaning: Problem with the temperature sensor (NTC) that monitors water temperature.
- Possible Causes: Faulty wiring to the sensor, faulty NTC sensor, faulty main control board.
- What You Can Try:
- Perform the power cycle described above.
- Professional Repair Likely Needed: Checking sensor resistance and voltage requires echnical expertise and tools. The sensor or main board may need replacement.
- Technical Detail: NTC resistance should be ~4.5-4.9 KΩ at 25°C/77°F.
E02: Heating Element Error
- Meaning: The machine is not heating the water correctly.
- Possible Causes: Damaged wiring to the heater, faulty heating element, faulty main control board.
- What You Can Try:
- Perform a power cycle.
- Professional Repair Likely Needed: Testing the heater’s resistance or replacing the element or main board requires a technician.
- Technical Detail: Heater resistance is typically around 28 Ω.
E03: Heater Relay Stuck Error
- Meaning: A component on the main control board related to the heater is faulty.
- Possible Causes: Faulty main control board.
- What You Can Try:
- Perform a power cycle.
- Professional Repair Likely Needed: This almost always requires replacing the main control board. A technician should verify the heater (see E02) first.
E04: Continuous Fill Error
- Meaning: The machine keeps filling with water and doesn’t stop, or fills when it shouldn’t.
- Possible Causes: Damaged wiring, faulty water inlet valve (stuck open), faulty main control board (valve control circuit failure).
- What You Can Try:
- Turn off the water supply taps immediately to prevent flooding.
- Perform a power cycle.
- Check inlet hoses for kinks.
- Professional Repair Likely Needed: Testing or replacing the inlet valve or main board is necessary.
- Technical Detail: Inlet valve resistance is typically around 3.7 KΩ.
E05: Drain Pump Error
- Meaning: The machine is unable to drain water.
- Possible Causes: Clogged drain pump filter, blockage in the drain hose, faulty wiring to the pump, faulty drain pump, faulty main control board.
- What You Can Try:
- Clean the drain pump filter (most common cause!).
- Check the drain hose for blockages or kinks.
- Perform a power cycle.
- Professional Repair Likely Needed: If the filter and hose are clear, the pump or main board may need testing or replacement.
- Technical Detail: Drain pump coil resistance is typically around 170 Ω.
E06 / E11: Motor Error (Universal DC or BLDC)
- Meaning: Problem with the main drive motor that spins the drum. (E06 often relates to the control circuit, E11 to the motor itself – different motor types exist: Universal DC or Brushless DC (BLDC)).
- Possible Causes: Faulty wiring/connectors, worn motor carbon brushes (Universal DC motors only), faulty motor tachometer (speed sensor), faulty thermal fuse on the motor, faulty motor itself, faulty motor control board (DC board or Inverter), faulty main control board.
- What You Can Try:
- Perform a power cycle.
- Check if the drum can be turned freely by hand (when off and empty). If it’s stuck, there might be an obstruction.
- Professional Repair Likely Needed: Diagnosing motor issues (checking resistance, tachometer, brushes, boards) is complex and requires a technician.
- Technical Details (Examples): Universal DC Motor Tachometer ~79Ω, Rotor ~4.3Ω. BLDC Motor phase resistance ~5-7Ω.
E07 / E27: Water Level Sensor Error
- Meaning: Problem with the sensor that detects the amount of water in the drum (Pressure Sensor). E27 can also indicate an overflow or flowmeter issue (see E12, E15).
- Possible Causes: Faulty wiring, blocked pressure chamber (where the sensor hose connects to the tub), damaged/kinked pressure sensor hose, faulty water level sensor, faulty main control board.
- What You Can Try:
- Perform a power cycle.
- Check the thin hose running from the drum area to the pressure sensor (if visible/accessible) for kinks or damage.
- Professional Repair Likely Needed: Cleaning the pressure chamber or testing/replacing the sensor or main board requires a technician.
- Technical Detail: Sensor operates on 5Vdc, frequency varies with pressure.
E08: Water Inlet Valve Error (Not Opening)
- Meaning: The machine isn’t filling with water or filling too slowly.
- Possible Causes: Water taps turned off, kinked inlet hoses, blocked filter screens inside the inlet hose connections, faulty wiring, faulty water inlet valve (not opening), faulty main control board.
- What You Can Try:
- Ensure water taps are fully open.
- Check inlet hoses for kinks.
- Turn off taps, disconnect hoses from the machine, and check/clean the small filter screens inside the connection points.
- Perform a power cycle.
- Professional Repair Likely Needed: If the above doesn’t work, the inlet valve or main board may need testing or replacement.
- Technical Detail: Inlet valve resistance is typically around 3.7 KΩ.
E09 / E10 / E23 / E28: Door Lock Error
- Meaning: Problem with the door locking mechanism or the signal confirming it’s locked/unlocked. (E09/E10 often relate to the control circuit, E23 to the switch itself, E28 to loss of locked signal).
- Possible Causes: Door not closed properly, obstruction in the door seal, faulty wiring, faulty door lock mechanism (interlock), faulty main control board.
- What You Can Try:
- Open the door and close it firmly, ensuring no clothes are trapped.
- Check the door catch and the lock area for any visible obstructions or damage.
- Perform a power cycle.
- Professional Repair Likely Needed: Testing or replacing the door lock assembly or main board requires a technician.
- Technical Detail: Door lock PTC resistance is ~989 Ω at 25°C/77°F.
E12 / E27: Water Leakage Error / Overflow Error
- Meaning: Water has been detected in the base of the machine (if equipped with an aqua-stop leak sensor – E12) or the water level is too high (E27).
- Possible Causes: Leak from a hose, pump, seal, or tub; Faulty inlet valve (see E04); Faulty pressure sensor (see E07); Malfunctioning aqua-stop switch.
- What You Can Try:
- Turn off water supply taps.
- Unplug the machine.
- Carefully tilt the machine (following manual instructions if available) to drain water from the base pan, which might reset the aqua-stop switch.
- Inspect hoses (inlet, drain, internal if visible) for obvious leaks or loose connections.
- Professional Repair Likely Needed: Finding and fixing the source of a leak or diagnosing overflow causes often requires disassembly by a technician.
E13: Inverter Module Communication Failure (BLDC Motors)
- Meaning: Communication error between the main control board and the inverter board that controls the BLDC motor.
- Possible Causes: Faulty wiring between boards, faulty inverter board, faulty main control board.
- What You Can Try:
- Perform a power cycle.
- Professional Repair Likely Needed: Requires diagnosis and potential replacement of boards or wiring by a technician.
E14: Jet Pump Error (Recirculation)
- Meaning: Problem with the recirculation pump (if fitted) that sprays water onto the clothes from the top of the drum area.
- Possible Causes: Faulty wiring, clogged filter for the jet system (if separate), faulty jet pump, faulty main control board.
- What You Can Try:
- Perform a power cycle.
- Check if your model has a specific filter for this system that needs cleaning (refer to manual).
- Professional Repair Likely Needed: Testing or replacing the pump or main board.
- Technical Detail: Jet pump coil resistance is typically around 160 Ω.
E15 / E27: Water Liter Counter / Flowmeter Error
- Meaning: Problem with the device (flowmeter) that measures the amount of water entering the machine (E27 can also relate to level sensor or overflow).
- Possible Causes: Faulty wiring, faulty flowmeter (reed switch or turbine issue), faulty main control board.
- What You Can Try:
- Perform a power cycle.
- Professional Repair Likely Needed: Requires testing voltage/signal from the flowmeter or replacing the flowmeter or main board.
E17: Over Foaming Warning
- Meaning: Too many suds/foam detected, likely interfering with the wash process. The program may end without a final spin.
- Possible Causes: Using too much detergent, using the wrong type of detergent (non-HE in a High-Efficiency machine).
- What You Can Try:
- Run a rinse and spin cycle or a cleaning cycle with no detergent to clear excess suds.
- Use less detergent in future washes.
- Ensure you are using High-Efficiency (HE) detergent if required by your model.
- No Repair Needed: This is a usage issue, not a machine fault.
E18: Unbalanced Load Warning
- Meaning: The load inside the drum is unevenly distributed, preventing the machine from safely reaching high spin speeds. The program may end without a final spin or with reduced spin speed.
- Possible Causes: A single heavy item, items tangled together, insufficient load size.
- What You Can Try:
- Open the door, redistribute the laundry items more evenly in the drum.
- Add a couple of similar items (like towels) if the load is very small.
- Remove some items if the machine is overloaded.
- Restart a “Spin” or “Drain & Spin” cycle.
- No Repair Needed: This is a usage issue, not a machine fault. Adjust loading practices.
E22: LCD Communication Failure Error
- Meaning: Communication problem between the main control board and the display/user interface board.
- Possible Causes: Faulty wiring connection, faulty user interface board, faulty main control board.
- What You Can Try:
- Perform a power cycle.
- Professional Repair Likely Needed: Requires checking connections and potential replacement of either board by a technician.
E24: Fill Sensor Error (Specific Type)
- Meaning: Problem with a specific type of load detection sensor, sometimes integrated with shock absorbers.
- Possible Causes: Faulty sensor connection, faulty sensor/shock absorber assembly, faulty sensor board, faulty main control board.
- What You Can Try:
- Perform a power cycle.
- Professional Repair Likely Needed: Requires technical diagnosis and potential part replacement.
E26: EEPROM Error
- Meaning: Error with the memory chip on the main control board that stores program settings.
- Possible Causes: Faulty main control board.
- What You Can Try:
- Perform a power cycle.
- Professional Repair Likely Needed: Almost always requires replacement of the main control board.
E29: Voltage Out of Limit Error
- Meaning: The incoming mains electrical voltage is too high or too low for the machine to operate safely.
- Possible Causes: Fluctuation or problem with your home’s electrical supply, faulty main control board (less likely).
- What You Can Try:
- Perform a power cycle.
- Check if other appliances in your home are affected by power issues.
- Consider plugging the machine into a different outlet (if feasible and safe).
- Wait for the power supply to stabilize if there’s a known local issue.
- Professional Repair Likely Needed: If the home’s voltage is confirmed to be stable and within range, the main board might be faulty. An electrician may be needed to check the house supply.
E31 / E32: Dryer NTC Sensor Error (Washer-Dryers)
- Meaning: Problem with the temperature sensor(s) used during the drying cycle (E31 dryer temp, E32 foam temp/safety).
- Possible Causes: Faulty wiring, faulty NTC sensor(s), faulty main control board.
- What You Can Try:
- Perform a power cycle.
- Ensure dryer filters/condensers are clean, as overheating can sometimes trigger sensor issues.
- Professional Repair Likely Needed: Requires testing sensor resistance/voltage and potential replacement of sensor(s) or main board.
- Technical Detail Examples: Dryer NTC ~840 Ω at 70°C/158°F. Foam NTC ~1.7 KΩ at 50°C/122°F.
E35 / E41 / E45: Dryer Heating/Fan/Overheat Error (Washer-Dryers)
- Meaning: Issue with the drying system’s heater (E35), fan (E41), or overheating protection (E45).
- Possible Causes: Blocked dryer lint filter or condenser unit, faulty wiring, faulty dryer heating element, faulty safety thermostats, faulty dryer fan motor or capacitor, faulty main control board (relay issues).
- What You Can Try:
- Thoroughly clean the lint filter(s) and the condenser unit (if applicable to your model – check manual). Poor airflow is a common cause.
- Perform a power cycle after cleaning and allowing the machine to cool down.
- Professional Repair Likely Needed: If cleaning doesn’t help, testing/replacing the heater, thermostats, fan, capacitor, or main board is necessary.
E37 / E38: Drum / NTC Overheating Warning (Washer-Dryers)
- Meaning: The machine detected excessively high temperatures, possibly during drying (E37 general, E38 specific sensor).
- Possible Causes: Blocked airflow (see E35), extended drying cycles, faulty sensor or thermostat.
- What You Can Try:
- Clean filters/condenser thoroughly.
- Allow the machine to cool down completely (at least 60 minutes) before trying again.
- Reduce drying load size or drying time.
- No Immediate Repair Needed (usually): Focus on cleaning and usage habits. If persistent, a sensor/thermostat check (professional) may be needed.
E45 (Variant) / E84: Configuration / Network Error
- Meaning: Problem with the machine’s internal configuration file (E45 variant) or network card (E84, for smart/connected models).
- Possible Causes: Corrupted software/firmware, faulty main control board, faulty network module.
- What You Can Try:
- Perform a power cycle.
- For E84, check your home Wi-Fi network connection (if applicable).
- Professional Repair Likely Needed: Often requires main board replacement or potential firmware update by a technician.
Advanced Diagnostics: Beko Washing Machine Test Mode
Warning: This mode is primarily intended for service technicians. Activating and running test mode incorrectly could potentially cause issues. Proceed with caution and only if you understand the risks.
Purpose: Test Mode cycles through the machine’s main components (valves, motor, heater, pump, etc.) to help pinpoint hardware failures.
Before Starting Test Mode:
- Switch the appliance OFF using the ON/OFF button.
- Ensure the drum is completely empty.
- Close the appliance door securely.
How to Activate Test Mode (Common Method – may vary slightly by model):
- Press and HOLD the Prewash button AND the Anti Crease button (or equivalent function buttons, often the first two function buttons) simultaneously.
- While holding these buttons, press the ON/OFF button to switch the machine on.
- Keep holding the function buttons until “TEST” (or similar indication like blinking lights) appears on the display, confirming Test Mode is active.
- The door should lock, and the lock icon will likely appear.
- Press the Start/Pause button once to begin the sequence of tests.
- Pressing Start/Pause repeatedly usually skips to the next test in the sequence.
Test Cycle Sequence (Example – order and exact tests vary by model):
- Error Code Discovery: Displays “E–” if no recent errors are stored. If errors exist, “E XX” shows the most recent/critical. Turning the program selector knob may cycle through previously logged errors.
- Software Version Check: Displays the version number of the main control board’s software.
- Display Test: All LEDs and display segments should light up or blink.
- Water Level Sensor / NTC / Voltage Check: Internal checks of sensor readings and system voltage.
- Motor Low-Speed Clockwise: Drum rotates clockwise at low speed (e.g., ~52 rpm).
- Motor Low-Speed Counter-Clockwise: Drum rotates counter-clockwise at low speed (e.g., ~52 rpm).
- Motor High-Speed Spin: Motor ramps up to maximum spin speed.
- Steam Inlet Valve Check: (Skips if no steam function) Tests the steam valve.
- Steam Heating Element Check: (Skips if no steam function) Tests the steam heater.
- Prewash Inlet Valve Check: Tests the valve supplying the prewash detergent compartment.
- Main Wash Inlet Valve Check: Tests the valve supplying the main wash detergent compartment.
- Detergent Box / Siphon Check: (Often combined with valve tests) Checks water flow through the drawer.
- Hot Water Inlet Valve Check: (If applicable) Tests the hot water valve.
- Water Heating Element / Pressure Switch / Flowmeter Check: Heats water (if applicable) and checks related sensors.
- Drain Pump Motor Check: Activates the drain pump.
- Jet Pump Control Check: (If applicable) Tests the recirculation pump.
- Error Display (During Test): May display errors detected during the test cycle.
- Cycle Completion Count: May show how many test cycles were run without errors.
How to Deactivate Test Mode:
- Method 1: Press and hold the ON/OFF button for about 3 seconds.
- Method 2: Unplug the appliance from the power outlet.
Beko Washing Machine Error Codes Summary
Error Code(s) | Meaning |
---|---|
E01 | NTC Sensor Error (Water Temperature Sensor) |
E02 | Heating Element Error |
E03 | Heater Relay Stuck Error (Main Board) |
E04 | Continuous Fill Error (Valve Stuck Open / Control) |
E05 | Drain Pump Error (Unable to Drain) |
E06 / E11 | Motor Error (Universal DC or BLDC Motor / Control) |
E07 / E27 | Water Level Sensor Error (Pressure Sensor) |
E08 | Water Inlet Valve Error (Not Opening / Filling) |
E09 / E10 / E23 / E28 | Door Lock Error (Mechanism / Switch / Control) |
E12 / E27 | Water Leakage Error (Aqua-stop) / Overflow Error |
E13 | Inverter Module Communication Failure (BLDC Motors) |
E14 | Jet Pump Error (Recirculation Pump, if fitted) |
E15 / E27 | Water Liter Counter / Flowmeter Error |
E17 | Over Foaming Warning (Too many suds) |
E18 | Unbalanced Load Warning |
E22 | LCD Communication Failure Error (Display Board) |
E24 | Fill Sensor Error (Specific Load Sensor Type) |
E26 | EEPROM Error (Main Board Memory) |
E29 | Voltage Out of Limit Error (Power Supply Issue) |
E31 / E32 | Dryer NTC Sensor Error (Washer-Dryers) |
E35 / E41 / E45 | Dryer Heating / Fan / Overheat Error (Washer-Dryers) |
E37 / E38 | Drum / NTC Overheating Warning (Washer-Dryers) |
E45 (Variant) / E84 | Configuration / Network Error (Main Board / Wi-Fi) |
When to Call a Professional
While some error codes point to simple fixes like cleaning a filter (E05) or adjusting the load (E18), many indicate potential faults with internal components like sensors, valves, motors, heaters, or the main control board.
You should call a qualified appliance repair technician if:
- You’ve tried the basic checks and the power cycle, but the error persists.
- The error code suggests a fault with an internal component (heater, motor, sensor, board).
- You see signs of water leakage (E12).
- You are uncomfortable or unsure about performing any troubleshooting steps beyond basic cleaning or checks.
- The machine behaves erratically, makes loud unusual noises, or has any signs of electrical issues (smells, sparks).
Remember: Attempting complex repairs yourself without proper knowledge and tools can be dangerous and may cause further damage to your appliance.
By understanding these Beko washing machine error codes and knowing when to perform simple checks versus calling for help, you can manage issues with your Beko washing machine more effectively.